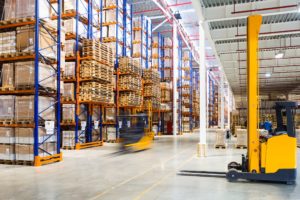
iStock.com/petinovs
Adding extra warehouses to your business provides many benefits such as reducing shipping costs, increasing storage capacity, and having warehouses for specific purposes to simplify warehouse management. However, the more warehouses you have, the more challenges you may have to deal with. Here are some of the most common challenges with managing multiple warehouses and how you can manage multiple warehouses effectively to overcome these challenges.
Failing to Review Processes
One of the biggest challenges when dealing with multiple warehouses is deciding whether to keep existing practices that you are comfortable with or apply a one-size-fits-all model to your new warehouses. If you are not open to new technology and automation, your processes can be hindered, and you warehouse management can become chaotic and disorganized. An inventory management solution that is agile and scalable can help your business as it grows to ensure that all your processes are organized well and that they can be integrated with other technologies.
Barcode technology and radio frequency identification tags are two examples of technology that are making multiple warehouse more manageable. By placing these two technologies on each product in your inventory, you can reduce or eliminate the problems associated with having documentation pass through multiple hands. Inventory management solutions increase efficiency, reduce errors, and allow you to integrate with other systems.
Increase in Web Site Traffic
As your business grows, you should be aware of how it affects your web site. Having more warehouses and more products often means more orders from customers. Make sure that your web site has the bandwidth to allow for more traffic. Even a few seconds of lagging on your site can significantly impact your sales. You should make sure that your web site can handle sudden increases in activity and work with your web developer or hosting provider as you scale.
Keeping Product Quality High
As you bring on more warehouses, you may have to adjust the method in which your products are manufactured to keep up with the increase in customer demand. The challenge with this, however, is that you may compromise product quality, get obsessed with meeting demand, or start allowing your partners to cut corners.
As you scale, you should be clear about your expectations and make sure that you are working with a team who can meet them. If your provider is unable to maintain quality and increase demand, you should be looking for a new third-party logistics provider.
Difficulty with Inventory Management
Inventory management is a challenging process on its own, especially when it comes to tracking every single item in your warehouse and analyzing it to find out its success with customers. By adding multiple warehouses to your supply chain, inventory management becomes even more complex. However, a reliable inventory management system that increases visibility and traceability will enable your business to see every item in each of your locations as they go from point A to point B.
Real-Time Collaboration between Multiple Warehouses
Multiple warehouses allow you to organize your inventory in a way that helps your business be more effective. You can provide specific products to certain customers in an area by placing a warehouse in that location, or spread out your inventory across the multiple channels to provide the same products to a larger region. Since warehouses tend to be located far from each other, it becomes challenging to establish real-time collaboration. Messages can be lost or misunderstood, and the lack of direct collaborations can limit organic discussions around refining processes and reorganization.
By working with a third-party logistics provider, you will benefit from a system that has integrated tools for communication and real-time collaboration. These features can help you mitigate issues around miscommunication, so that everyone in your company knows what is happening as it happens.
Connecting with e-Commerce
Customers who want to shop for your products online expect to know if the products are available and when they will arrive after ordering. A robust inventory management system that lets you monitor your stock levels across each sales channel will let you deliver this information to your customer and uphold that promise. However, multiple warehouses can make this challenging to fine-tune. Therefore, full visibility into inventory stock is important to help you know exactly which products you should order more of and which products you should slow down on manufacturing. You will also be able to provide an accurate item count when your customers visit your online store to help them manage their expectations.
Unable to Focus on Bigger Growth Goals
Managing multiple warehouses can be challenging when you get swamped with too many tasks and cannot focus on bigger growth initiatives. Chances are that you might need to hire more people to help you, whether it is for a temporary time or permanently. Consider all the tasks and responsibilities that you are managing on your own and figure out which of these tasks can be outsourced to someone else. Prioritize this list based on how important, impactful, and time-consuming each is.
You can also make a list of the things you wish you could do if you had more time. Taking time to create this list can help you make the right choices as you invest in new employees or a new service provider.
Contact APS Fulfillment, Inc. for Your Inventory and Warehouse Management Needs
Managing your inventory is one of the most important areas to consider as you add new warehouses to your business. However, the challenges don’t stop there. You also need to consider your web site, inventory management, maintaining good customer service, and keeping up with your sales and marketing responsibilities. All these tasks can seem overwhelming to manage with the team you currently have, which is why you should consider working with a third-party logistics provider who has the tools and experience to help you scale your business.
APS Fulfillment, Inc. is prepared to help our clients find the right solutions to meet their warehouse organization and inventory management needs. We provide services such as real-time inventory management, e-commerce fulfillment, fulfillment solutions, and fulfillment markets. There are endless benefits to working with a third-party logistics company that uses the best quality software systems to manage your warehouse, so if you’re looking for the right company, look no further than APS Fulfillment, Inc. You can contact us by e-mail at [email protected] or by phone at (954) 582-7450.