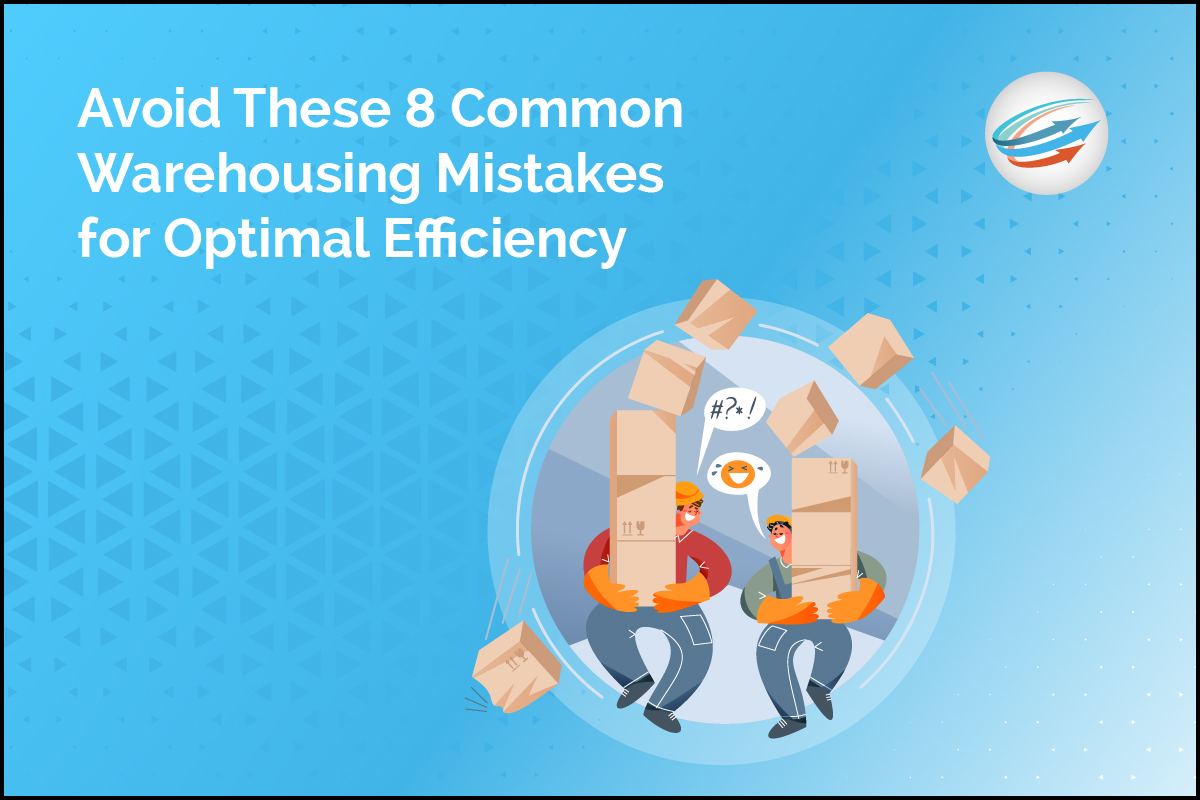
Efficient warehousing is the backbone of any logistics operation. Whether you run a small e-commerce venture with modest storage space or manage a sprawling warehouse for a regional distributor, the way you handle your inventory directly impacts your company’s bottom line. In reality, warehouses can be a source of unseen inefficiencies, eating into your profit margins and customer satisfaction.
This blog post is your guide to the 8 most common mistakes warehouse managers make and how to avoid them.
Avoid These Common Warehousing Mistakes
Inefficient Inventory Management
One of the most common mistakes in warehousing is inefficient inventory management. This includes both holding excess inventory and inaccurately tracking inventory. When businesses overstock inventory, it ties up valuable space and can lead to increased costs. Without accurate tracking, it’s difficult to know exactly what stock is on hand, leading to potential stockouts or over-ordering.
Poor Warehouse Layout
A poorly designed warehouse layout can have a significant impact on efficiency and productivity. Not optimizing space utilization can result in wasted space and difficulty locating items, while a disorganized layout can lead to longer picking times and increased labor costs. It’s important to have clearly designated areas for receiving and shipping to streamline processes.
Neglecting Technology
In today’s fast-paced world, relying on manual processes such as paper-based systems can significantly hinder warehouse operations. Investing in a Warehouse Management System (WMS) can greatly improve efficiency by automating tasks such as inventory tracking, order fulfillment, and data analysis. Utilizing data analytics from a WMS can also provide valuable insights for improving warehouse operations.
Overlooking Safety Practices
Maintaining a safe work environment should be a top priority in any warehouse setting. Neglecting safety practices can lead to accidents or injuries that not only harm employees but also disrupt operations. This includes inadequate employee training on safety procedures, such as proper lifting techniques or operating equipment safely. It’s also important to regularly maintain equipment to prevent malfunctions that could cause harm.
Lack of Staff Training
Properly trained staff is crucial to the success of a warehouse. Not providing adequate training on warehouse operations and equipment usage can lead to mistakes, inefficiencies, and safety hazards. It’s important to address the importance of accuracy and efficiency in training sessions, as well as the need for ongoing skills development. This can include cross-training employees on different tasks to ensure flexibility and continuity in operations.
Poor Communication and Collaboration
A lack of clear communication and collaboration between different departments and teams can result in confusion, delays, and errors in inventory management, order fulfillment, and customer service. Warehouse staff needs to communicate effectively to ensure accurate inventory levels and timely delivery of orders. Collaboration with suppliers and carriers is also crucial for efficient inbound and outbound logistics.
Inadequate Security Measures
Warehouse security is essential for protecting valuable inventory items from theft or damage. Not having proper access control systems in place can make it easier for unauthorized individuals to enter the warehouse and steal goods. Ignoring security protocols for valuable items can also put them at risk. It is important to implement security measures such as CCTV cameras, alarms, and secure storage areas to prevent theft or damage.
Neglecting Sustainability Practices
In today’s world, sustainability practices are becoming increasingly important in all industries, including warehousing. Neglecting sustainability practices can have a negative impact on the environment as well as the company’s reputation. Warehouses should aim to be more environmentally friendly by using energy-efficient equipment and lighting, exploring sustainable packaging options, and implementing proper waste management solutions.
How Can APS Fulfillment, Inc. Help Improve Your Warehouse?
APS Fulfillment, Inc. offers a range of services designed to improve your warehousing efficiency. With our warehouse management system, Extensiv, you can gain complete control and visibility over your warehouse operations, from order and inventory management to shipping and receiving.
Extensiv combines four industry-leading software—3PL Central, Scout, Skubana, and CartRover—into one comprehensive omnichannel fulfillment platform. It’s a tool that can transform your warehousing activities, making them more efficient and less prone to errors.
Contact APS Fulfillment, Inc. Today!
Warehousing might appear straightforward, but the intricacies lie in the details. By avoiding the above mentioned mistakes and investing in efficiency, you’re laying a solid foundation for your business to thrive.
Partnering with APS Fulfillment, Inc. ensures that you’re not only mitigating these errors but also securing a competitive edge in your industry. We offer full-service e-commerce fulfillment out of Miami that includes state-of-the-art warehouse management software.
Ready to streamline your warehousing? Take the first step and contact us today! E-mail at [email protected], visit our website at www.apsfulfillment.com, or call us at (954) 582-7450.