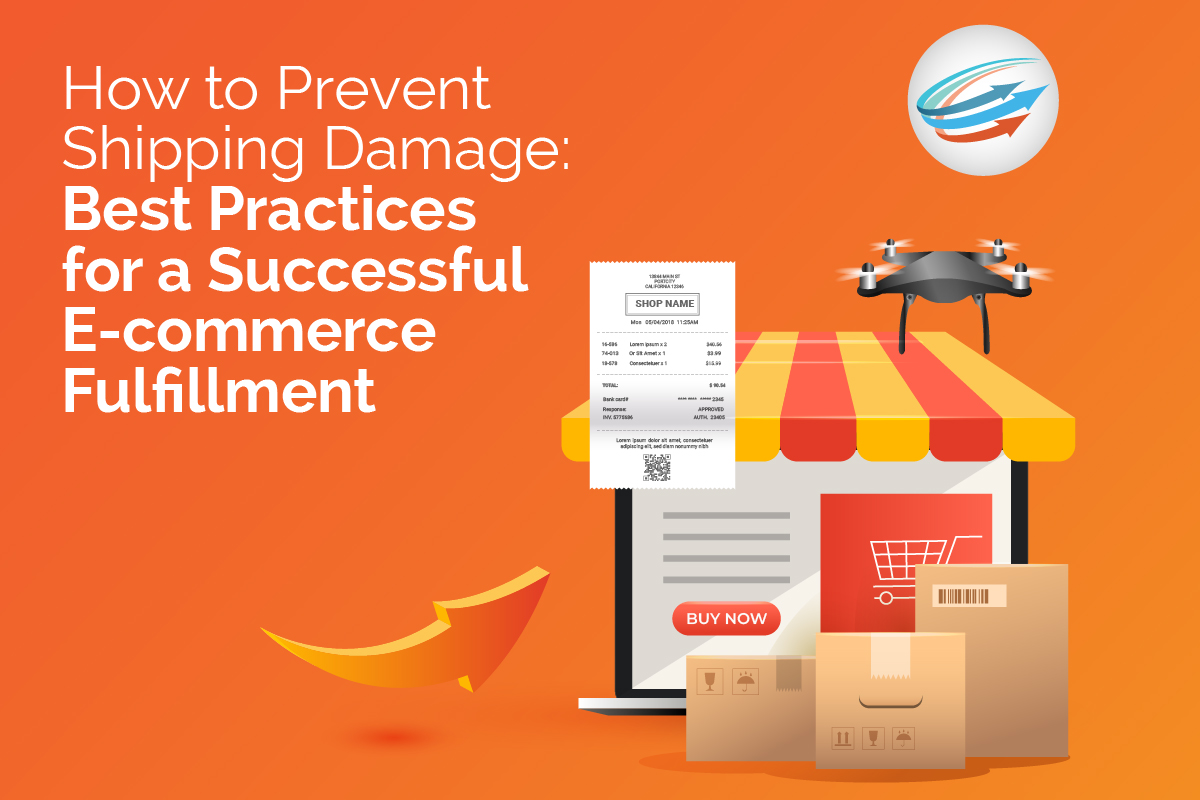
As an e-commerce business, maintaining your reputation and customer satisfaction can be highly dependent on the successful delivery of your products. But one key factor that is often overlooked is shipping damage—something you need to consider if you aren’t managing it properly. To ensure a positive shopping experience for your customers, preventing shipping damage should be at the top of your list when it comes to best practices for a successful e-commerce fulfillment process. In this blog post, we will discuss essential steps you can take to prevent goods from being damaged in transit, such as choosing the right packaging supplies and understanding common logistical challenges. Keep reading to learn more!
Understanding Common Causes of Shipping Damage
Shipping damage can be the bane of any online shopper’s existence. Nothing is worse than eagerly waiting for a package to arrive, only to open it up and find that its contents have been damaged in transit. While it’s impossible to completely eliminate the risk of shipping damage, there are certain common causes that can be avoided.
- Improper or Ill-Fitting Packaging: Without proper packaging, a product is vulnerable to damage from movement, pressure, impact, and unfavorable environmental conditions during transit, which many common carriers and warehouses might not have the expertise to ensure.
- Improper Handling: While there are myriad ways in which goods can become damaged during shipping, one of the most frequent culprits is improper handling. Freight handlers may unintentionally mistreat packages, which can lead to internal or external product damage, rendering it unusable or inefficient.
- Inaccurate Labeling: If packages are not labeled properly, it can cause confusion and delay during the shipping process. The wrong shipping address or information can lead the package to be sent to the wrong location—or worse, not sent at all.
- Water or Humidity Damage: Whether it’s because of heavy rain, subpar packaging materials, or long transit times in humid climates, moisture can wreak havoc on your shipments. It can cause warping, mold growth, rust, and other types of damage that can make your products unusable.
- Manufacturer Damages: This can occur when the item is not properly packaged or protected for transportation. While it may be tempting for manufacturers to cut corners when it comes to packaging, it’s important to ensure that the product is well-protected before it leaves the warehouse.
Related: How to Handle Damaged and Defective Products?
Proper Packaging Techniques
Below are some tips to ensure proper packaging when shipping goods for your e-commerce store.
- Select the Appropriate Packaging Materials: Different types of packages require different materials, and using the wrong type of material can lead to damaged goods. It’s important to select the right type of packaging material for your product, such as corrugated cardboard boxes for heavier items or bubble wrap for delicate items.
- Utilize Cushioning and Padding Effectively: Cushioning and padding are essential components of proper packaging techniques. Not only do they help to protect your product from shock and vibration during transit, but they also provide additional cushioning in case the package is dropped or mishandled.
- Ensure Secure Closures and Sealing: This helps to ensure that your package stays closed during transit and prevents any water or dust from entering the package. Common closure methods include tape, glue dots, shrink wrap, or strapping tape; however, some products may require a more secure method such as heat sealing.
- Label the Box as Fragile: It’s also important to label your box as fragile so that it receives special handling during transit. Labeling a box will alert carriers that there are delicate items inside and will help ensure that they handle it with care when loading it onto trucks or planes.
- Work with Reliable Carriers: Make sure to research different carriers and look into their delivery times, customer service ratings, pricing structure, insurance coverage policies, etc., in order to find one that best suits your needs. Additionally, make sure that they have experience handling packages containing fragile items!
Work with a 3PL Provider like APS Fulfillment, Inc.
When it comes to e-commerce fulfillment, preventing shipping damage is crucial. No one wants to receive a package that has been broken or damaged in transit. That’s why it’s vital to partner with a 3PL provider who knows how to mitigate shipping damage and ensure customer satisfaction.
At APS Fulfillment, Inc., we take this responsibility seriously. Our team of experts has years of experience in the industry and knows all the best practices for successful e-commerce fulfillment. From careful packaging to accurate labeling and handling, we make sure that products arrive at their destination in pristine condition.
If you’re looking for the right company to partner with, look no further than APS Fulfillment, Inc. You can contact us by e-mail at [email protected] or by phone at (954) 582-7450.