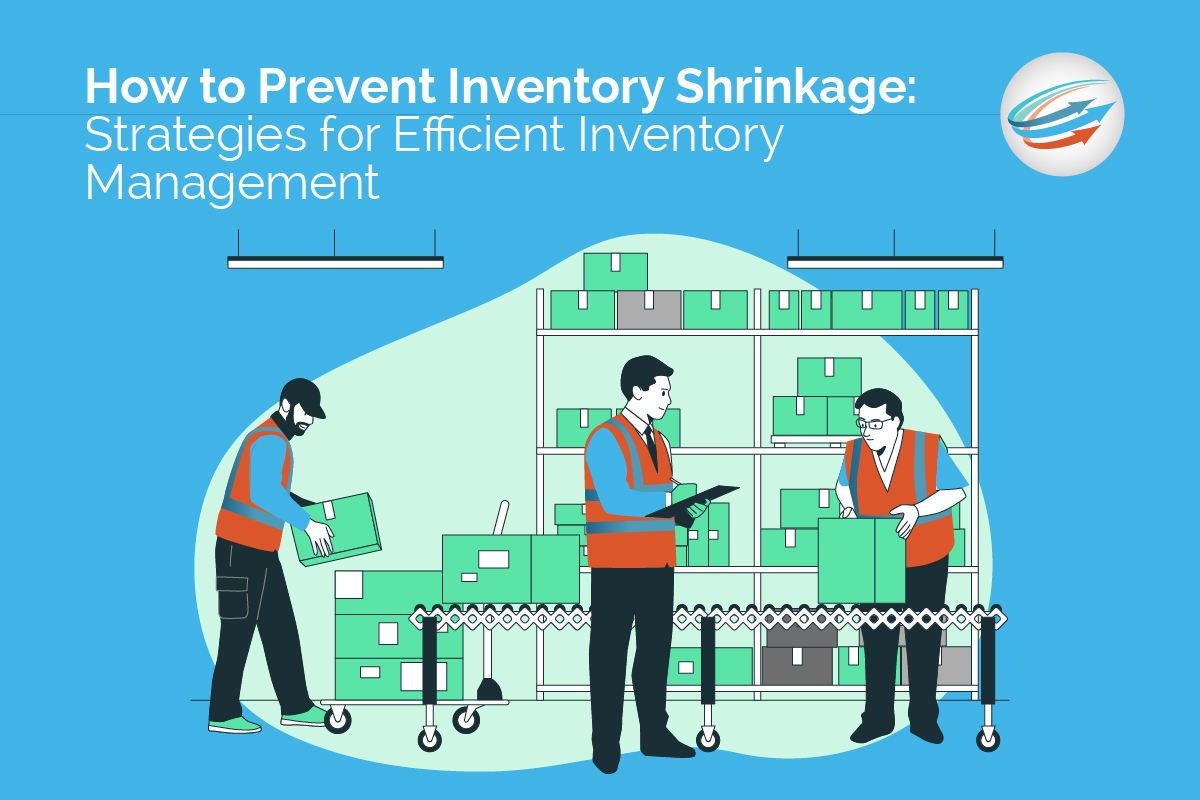
Running an e-commerce business isn’t easy, especially with the many hurdles that can crop up in inventory management processes. One major issue is inventory shrinkage, which is when products mysteriously disappear or become damaged due to theft, mishandling, and other causes. While outright theft may be harder to prevent at times, you can proactively take steps to detect and prevent inventory shrinkage in other forms throughout your supply chain. In this blog post, we’ll explore various inventory shrinkage prevention tips so you can stop worrying about loss of goods and start focusing on growing your business instead!
Understanding Inventory Shrinkage
Inventory shrinkage is a common concern for businesses of all sizes. It refers to the loss of inventory due to various factors, such as:
- Employee Theft: Employee theft is one of the most common causes of inventory shrinkage. Employees may steal products for their own personal use or to sell on the black market.
- Shoplifting: Shoplifters may take items without paying for them or attempt to return stolen items for a refund.
- Shipping Errors: Shipping errors can also lead to inventory shrinkage if products are lost in transit or delivered to the wrong address due to incorrect labeling or other mistakes made by shipping companies.
- Human Error/Damage: If products are mishandled by employees or damaged during storage or transport due to improper handling it can also lead to inventory shrinkage.
- Inaccurate Record-Keeping: Inaccurate record-keeping can also lead to inventory shrinkage if records do not reflect actual product quantities in stock accurately due to data entry errors or other issues with the system used for tracking inventory levels.
The financial implications of inventory shrinkage can be significant, including lost revenue, reduced profitability, and increased costs associated with replacing lost inventory. It’s essential to understand the root causes of inventory shrinkage and take proactive measures to mitigate its impact on your bottom line.
Strategies to Prevent Inventory Shrinkage
To reduce inventory shrinkage, companies need to implement effective strategies, such as:
Robust Inventory Tracking Systems
Inventory management software can help businesses keep track of their inventory levels in real-time, allowing them to identify any discrepancies quickly and take corrective action. APS Fulfillment, Inc. offers a range of inventory tracking solutions that can be tailored to meet the needs of any business. With these tools, businesses can monitor their stock levels, manage orders, and streamline the entire supply chain process.
Employee Training and Accountability
Employees should be trained on efficient inventory management practices such as how to properly count items, how to record changes in inventory levels, and other important procedures related to managing inventory. In addition, employees should be held accountable for their actions; this will help ensure that they take their responsibilities seriously and take steps to prevent theft or errors.
Security Measures
Security measures are a big part of inventory damage prevention. Surveillance cameras, access control systems, and secure storage areas can all help to deter theft or errors from occurring in the first place. At APS Fulfillment’s facilities, security is always a top priority; our warehouses are equipped with state-of-the-art surveillance systems and access control measures so that you can rest assured your products are safe at all times.
Regular Audits and Reconciliation or Surprise Audits
Regular audits and reconciliations are essential for maintaining accurate records of inventory levels. This helps businesses identify discrepancies between actual stock levels and what is recorded in the system quickly so that corrective action can be taken promptly if necessary. Additionally, surprise audits can be an effective way of deterring internal theft or errors; unannounced checks ensure that employees remain vigilant when it comes to following proper procedures when handling products or recording changes in stock levels.
Split Responsibilities
By assigning different tasks to different people within an organization, there is less risk of one person having too much control over the process which could lead to fraud or errors occurring unnoticed over time. This approach also ensures that everyone involved has a vested interest in maintaining accurate records as they will all be held accountable for any discrepancies found during regular audits or reviews
Work with a 3PL (Third-Party Logistics) Provider
By partnering with a third-party logistics provider like APS Fulfillment, Inc., businesses can outsource inventory management tasks and gain access to a range of benefits. For instance, 3PL fulfilment solutions can enhance security and accuracy through the implementation of advanced inventory tracking software and strict quality control protocols. By taking these steps, businesses can reduce the risk of inventory shrinkage and enjoy greater peace of mind knowing that their products are in good hands.
Choose APS Fulfillment, Inc. to Reduce Inventory Shrinkage
Seeking expert support is a smart move for businesses looking to improve their inventory control. APS Fulfillment, Inc. is a reliable partner that offers end-to-end inventory management solutions. With our advanced technology, experienced team, and customer-centric approach, APS Fulfillment Inc. can help businesses reduce inventory shrinkage, streamline their operations, and achieve better bottom-line results.
Don’t wait until inventory shrinkage becomes a crisis. Take action now and partner with APS Fulfillment for effective inventory control. Get in touch with us today and one of our consultants will tailor a fulfillment plan that will help grow your business. To book a consultation, call (954) 582-7450 or email [email protected].
Also Read: What Is Supply Chain Mapping and Why Is It Important for E-Commerce Businesses?