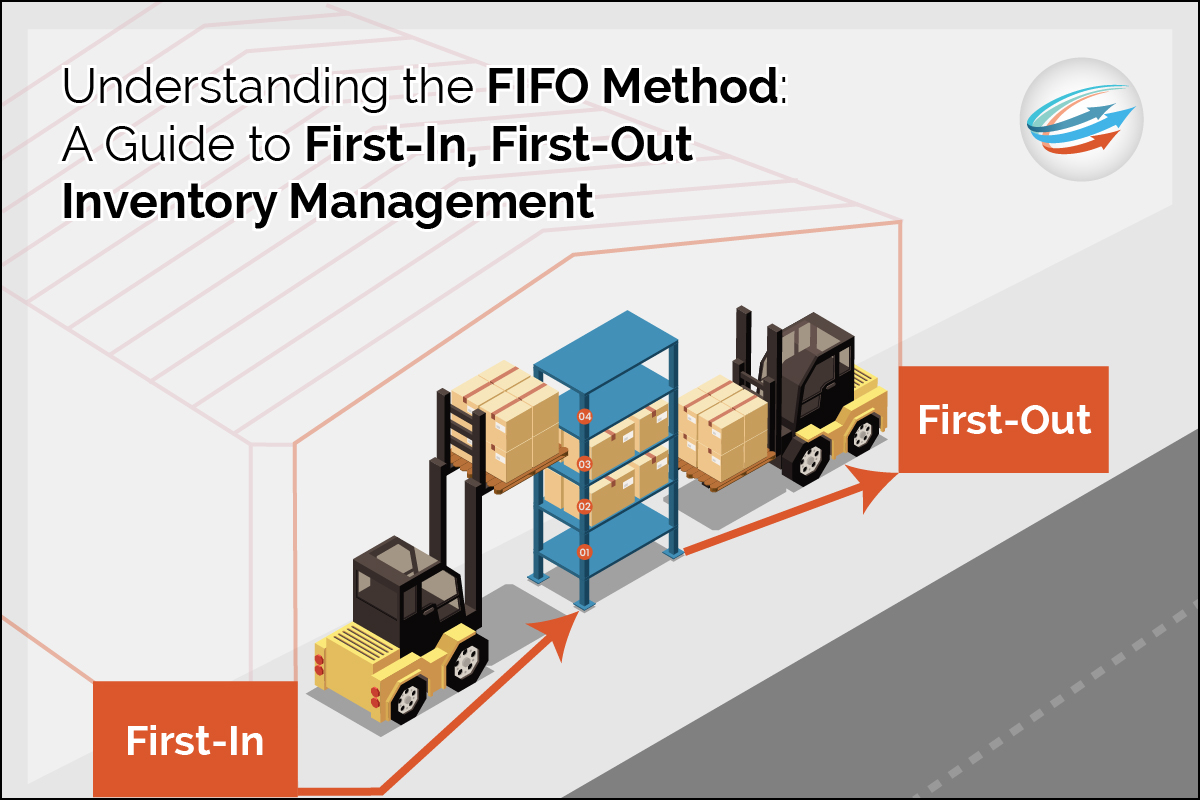
Navigating the complex world of inventory management can be daunting, especially for small business owners, warehouse managers, and retailers. In an era where efficient supply chain and fulfillment operations are critical, understanding the FIFO method—First-In, First-Out—can make a significant difference.
This guide aims to shed light on how businesses, particularly those dealing with perishable goods, can benefit from this tried-and-true inventory management technique.
What Is the FIFO Method?
The FIFO inventory method, or First-In, First-Out, is an approach where the first items added to inventory are the first ones to be used or sold. This logical flow ensures that older stock is moved before newer stock, maintaining product freshness and quality.
In practical terms, FIFO is particularly valuable in preventing spoilage and waste, with a study showing that approximately 60% of food waste results from ineffective inventory management. Implementing First-In, First-Out inventory can significantly reduce this figure, especially in industries where products have a limited shelf life.
When comparing FIFO vs. LIFO (Last-In, First-Out), FIFO is indispensable for optimizing operations and minimizing losses. While LIFO can be useful in certain situations, it often leads to older stock being left unused, potentially resulting in waste. On the other hand, FEFO (First-Expired, First-Out) focuses on expiration dates, which is crucial for certain industries but requires meticulous tracking systems.
Key Benefits of Using the FIFO Method
Reducing Obsolescence and Waste
FIFO’s design inherently minimizes spoilage, making it especially relevant for industries like food, pharmaceuticals, and consumer goods. Businesses using the FIFO method report a reduction in product obsolescence by up to 15%, translating to substantial savings and reduced losses. By prioritizing older stock, companies can ensure that items are sold or used before they become unsellable.
Maintaining Accurate Financial Statements
One of the lesser-discussed benefits of FIFO is its impact on financial accuracy. In times of inflation, First-In, First-Out inventory provides a clearer picture of the cost of goods sold (COGS), leading to more accurate accounting and tax reporting. A PwC study indicates that companies that adopt FIFO improve their financial accuracy by 20% in volatile pricing environments.
Better Inventory Visibility
With FIFO, businesses often experience enhanced inventory visibility, which leads to a more organized warehouse environment. When companies can better track stock movements, it becomes easier to manage orders, reduce errors, and maintain a steady supply chain flow.
Improved Cash Flow and Profitability
Implementing the FIFO inventory method allows businesses to make informed purchasing decisions, improving cash flow and profitability. Companies that optimize their inventory management systems, including FIFO usage, have reported a 35% increase in operational efficiency, underscoring the method’s economic advantages.
Industries That Benefit Most from FIFO
Food and Beverage
The food and beverage industry is one of the most prominent beneficiaries of FIFO. By ensuring that products with the closest expiration dates are prioritized, businesses can manage perishables effectively, reducing food waste and loss. With the industry losing $1 trillion annually due to waste, the FIFO method can help cut these losses by up to 20%.
Pharmaceuticals
In pharmaceuticals, adhering to compliance regulations and avoiding expired product issues is critical. FIFO plays an essential role by reducing waste and ensuring that products are dispensed in order of receipt. The method helps pharmaceutical companies reduce expired inventory by up to 30%.
Retail
For retailers, managing seasonal inventory can be challenging. FIFO helps prevent unsellable stock accumulation by prioritizing older inventory, ultimately leading to higher inventory turnover rates. Over 70% of e-commerce businesses report improved turnover after adopting First-In, First-Out inventory practices.
How to Implement the FIFO Method in Your Warehouse
Organizing Your Warehouse Layout
A well-organized warehouse layout is fundamental for successfully implementing FIFO. Structuring storage, such as using shelving systems and clear labeling, ensures that older stock is easily accessible and used first. Proper layout planning can prevent confusion and streamline operations.
Utilizing Warehouse Management Systems (WMS)
Leveraging technology is critical in modern inventory management. Warehouse Management Systems (WMS) can track inventory age and automate FIFO processes, significantly enhancing efficiency. Warehouses that use WMS report a 25% reduction in labor costs and a 50% increase in order accuracy, highlighting the importance of technology integration.
Employee Training and Processes
Training staff to follow FIFO principles when stocking and picking items is essential. Employees should understand the importance of FIFO in reducing waste and improving operational efficiency. Regular training sessions can reinforce these practices, ensuring consistent application.
Regular Audits and Inventory Checks
Conducting regular audits and inventory checks is vital to ensure FIFO is implemented correctly. Periodic reviews help identify any deviations from the method, allowing businesses to make necessary adjustments and maintain optimal inventory management practices.
Challenges of Implementing the FIFO Method
While the FIFO method offers numerous benefits, challenges can arise in its implementation. Warehouse layout and space management can be limiting factors, especially in businesses with high product variation.
Additionally, software and system requirements for tracking inventory may entail initial costs, though the long-term benefits often outweigh these expenses.
Best Practices for Managing FIFO Inventory
Implementing effective practices can maximize the benefits of FIFO. Efficient warehouse organization, including shelving and stock rotation, helps maintain order. Additionally, utilizing technology like warehouse management systems streamlines processes and enhances accuracy. Regular employee training ensures staff are aligned with FIFO practices, reinforcing the method’s value.
Partner with APS Fulfillment, Inc. for Effective Inventory Management Solutions
When it comes to navigating the complexities of inventory management, partnering with a trusted expert can make all the difference. APS Fulfillment, Inc. stands out as a leading choice in this arena, boasting a wealth of experience and innovative strategies tailored to meet diverse business needs.
Get in touch with us today and one of our consultants will tailor a fulfillment plan that will help grow your business. To book a consultation, call (954) 582-7450 or email [email protected] and see how we can provide guidance and support in implementing FIFO effectively.