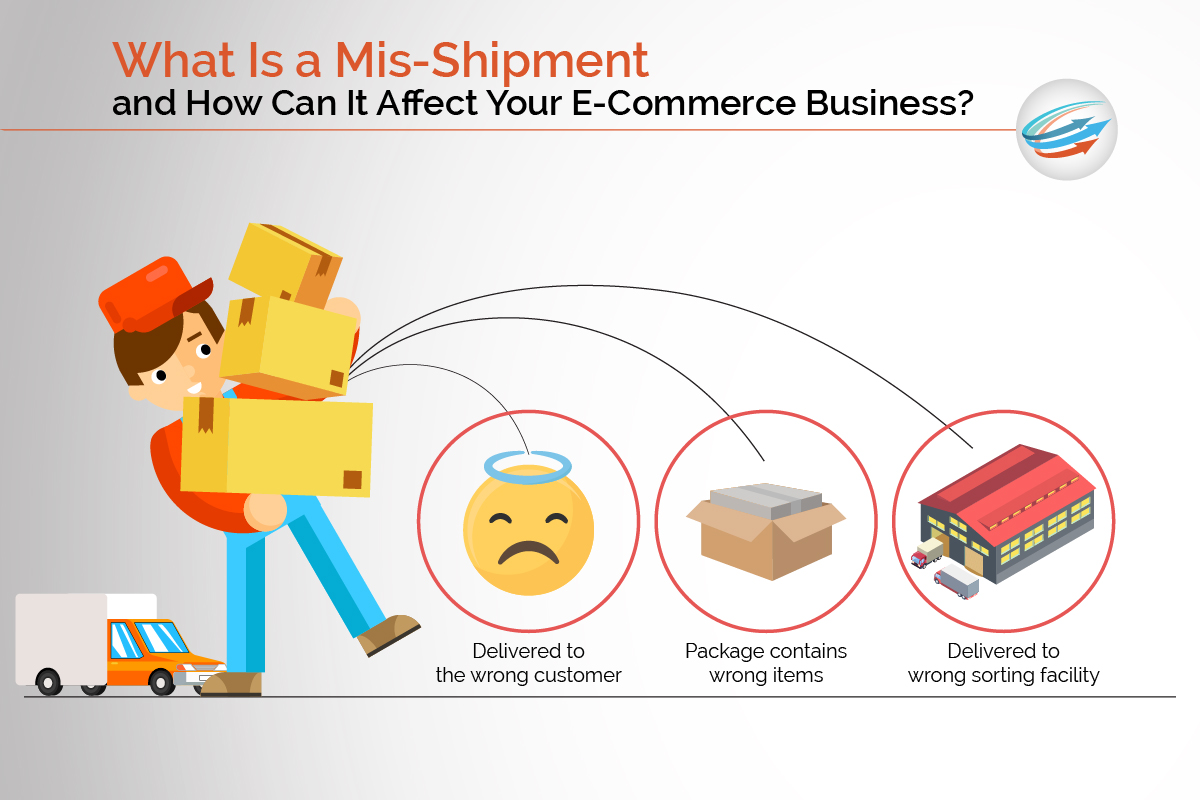
Every e-commerce business faces the challenge of mis-shipments from time to time. A mis-shipment occurs when the buyer receives an incorrect order, either due to the fault of the business or with no fault at all. This could include a different product being shipped out than expected, more items received than paid for, or damaged goods arriving to a customer.
Whether it was accidental or intentional, the financial cost of mis-shipments can be significant for both customers and businesses, including cost of shipping, labor, and time. In this blog post, we will explore how to reduce mis-shipments in your e-commerce business.
Why Do Mis-Shipments Happen?
Even with all the technology available to businesses today, mis-shipments still happen. Often times, mis-shipments occur due to mail carriers not processing packages correctly. This can manifest in several different ways including untimely sorting, misplaced labels, or inaccurate tracking information.
All of these errors can easily disrupt the entire shipping process and cause items to be misdirected or unclaimed by their rightful recipient. Ultimately, a thorough understanding of each step of the shipping process is key in reducing instances of mis-shipments.
What Are the Consequences of Mis-Shipments?
Mis-shipments can cause great frustration for both customers and business owners, and the consequences of such an event can be significant. Customers may find that they have not received the product they need after waiting a long period of time, potentially leading to cancelled orders.
Business owners who are responsible for mis-shipments not only risk alienating their customers with delays which affect the customer journey, but also incur financial losses through sorting out delivery issues as well as costs associated with refunding purchases or supplying replacements.
Ultimately, mis-shipments can be disruptive and expensive to deal with, creating problems both sides would rather avoid.
How Can Businesses Reduce Mis-Shipments?
To minimize the effects of mis-shipments, businesses must ensure a rigorous quality control process is in place throughout the supply chain. Below are some tips to consider:
- Conducting regular inventory checks and using barcode scanners for accurate picking will make sure the right items are being sent out
- Enacting quality control checks on a daily basis prior to shipment and having open communication with carriers will help ensure orders arrive in time
- Using a robust order management systems can also help streamline processes
- A fast returns process that is simple for customers to use will make it easier to react quickly
- Working with a reliable third-party logistics provider can prove beneficial since they can provide the expertise necessary to ensure successful deliveries
Contact APS Fulfillment, Inc. to Help Your Business Prevent Mis-Shipments
APS Fulfillment, Inc. offers full-service e-commerce fulfillment out of Miami that includes state-of-the-art warehouse management software (WMS). Get in touch with us and one of our consultants will tailor a fulfillment plan designed to grow your business. Book a consultation by calling (954) 582-7450 or email [email protected].