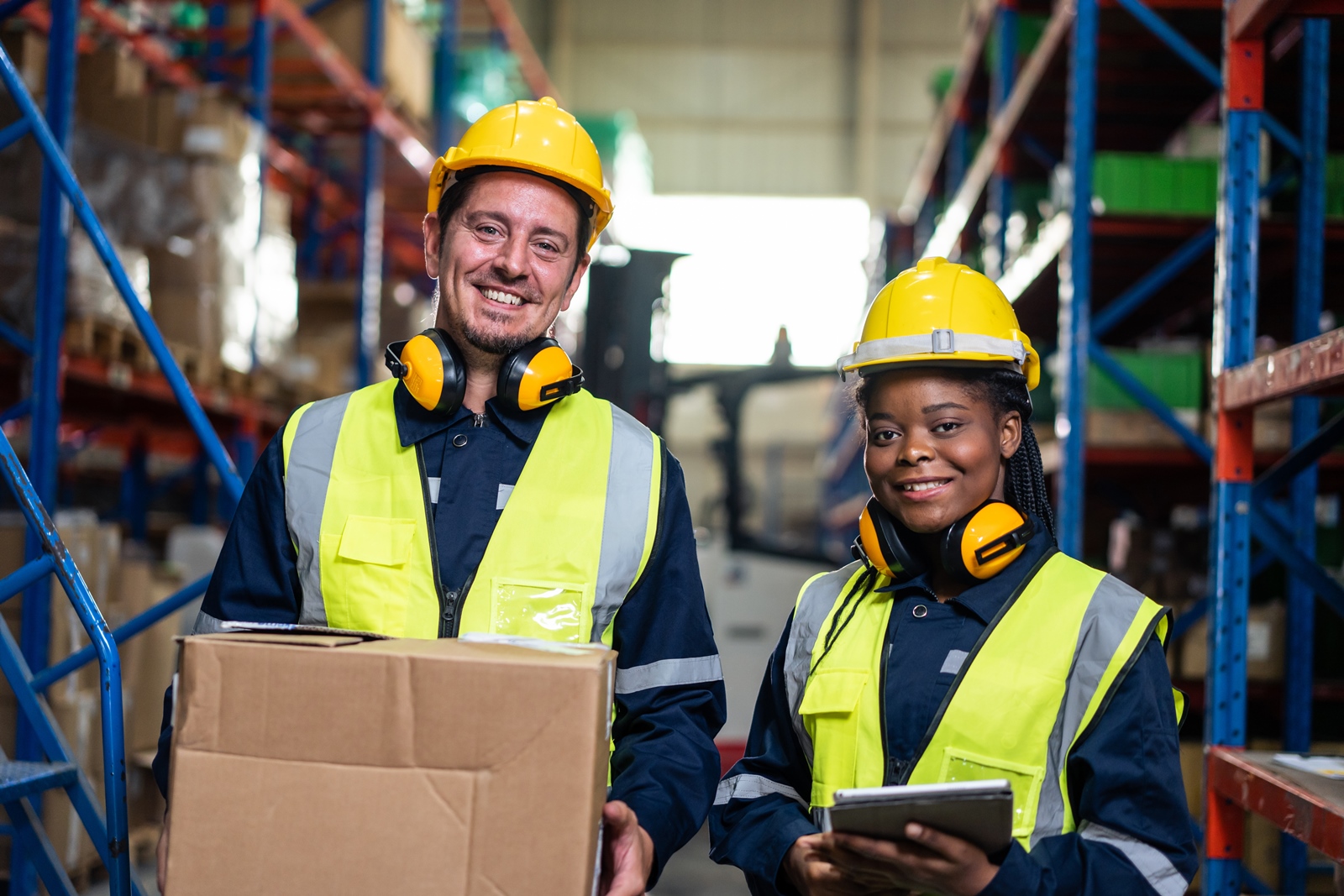
Efficient picking and packing are the beating heart of successful order fulfillment. For e-commerce businesses, logistics professionals, and warehouse managers, optimizing these processes can make the difference between delighting your customers or losing them to competitors. However, bottlenecks in picking and packing workflows are common and can pose significant challenges.
This blog will explore the most frequent picking and packing bottlenecks, provide actionable solutions to tackle them, and help optimize your warehouse operations for maximum efficiency.
Identifying Common Bottlenecks in Picking
Picking involves selecting the right products from inventory to fulfill customer orders. While this seems straightforward, inefficiencies in the picking process can lead to delays, errors, and increased costs.
Here are the most common picking bottlenecks and solutions to address them:
Inefficient Warehouse Layout
Poorly designed layouts with disorganized storage and excessive travel distances slow down pickers. They waste valuable time walking, searching for products, and managing obstructed pathways.
Solutions
- Analyze warehouse layout: Use traffic flow and heat maps to identify inefficiencies in movement.
- Logical zoning: Group products based on their picking velocity (i.e., fast-moving items closer to the shipping area).
- ABC analysis: Classify inventory into “A” (high frequency), “B” (moderate), and “C” (low frequency) categories and organize accordingly.
- Clear labeling: Ensure both shelves and containers are well-labeled for quick identification.
- Optimize storage systems: Invest in structured layouts like block stacking or racking to save space and reduce retrieval times.
Inaccurate Inventory Management
Stockouts, misplaced items, and phantom inventory lead to pickers struggling to locate products. Wasted time and canceled orders create operational chaos and unhappy customers.
Solutions
- Implement a robust inventory management system (IMS) or a warehouse management system (WMS).
- Conduct regular cycle counts to keep inventory data accurate.
- Use barcode scanners or RFID technology for precise real-time tracking of stock.
- Improve receiving and put-away processes to ensure items are stored in the correct location immediately upon arrival.
Inefficient Picking Strategies
Using suboptimal methods for picking can result in pickers making multiple trips or assembling orders inefficiently.
Solutions
- Analyze order patterns to adopt the best picking method for your warehouse. Options include:
- Batch picking: Picking multiple orders at once.
- Zone picking: Assigning pickers specific zones to streamline workflow.
- Wave picking: Combining batch and zone strategies for larger orders.
- Optimize pick paths to reduce unnecessary travel.
- Organize pick lists in a logical order to help pickers work efficiently.
Lack of Proper Equipment and Tools
Outdated or insufficient tools slow down picking and may cause errors or physical strain for employees.
Solutions
- Invest in ergonomic material handling equipment like carts, pallet jacks, or forklifts.
- Provide technology, such as scanners, label printers, and mobile workstations.
- Regularly inspect and maintain equipment to prevent downtime.
Poor Communication and Information Flow
Sampling errors occur when pickers work with outdated pick lists or unclear instructions.
Solutions
- Integrate order management and warehouse systems for real-time updates.
- Transition from paper to digital pick lists where possible.
- Use communication tools like two-way radios or messaging apps to relay updates instantly.
Identifying Common Bottlenecks in Packing
Packing is the last line of defense before your products head out the door. Inefficiencies at this stage can lead to delays, damaged goods, and customer dissatisfaction.
Inefficient Packing Stations
Disorganized workspaces and inaccessible tools/materials result in slow packing times.
Solutions
- Design ergonomic packing stations with everything needed within arm’s reach.
- Keep materials (boxes, tape, filling) systematically organized and restocked.
- Provide tools such as scales, tape guns, and label applicators.
- Implement standard operating procedures to create consistency.
Using Incorrect or Excessive Packaging Materials
Improper packaging increases shipping costs, wastes materials, and may damage products in transit.
Solutions
- Train packers to choose appropriate packaging for each item size and type.
- Use a box sizer or a packaging system to minimize void fill.
- Opt for sustainable packaging options that align with environmental goals while cutting costs.
Lack of Clear Packing Instructions
Ambiguous or missing instructions result in errors such as shipping incorrect items or failing to meet requirements for special orders or kitting.
Solutions
- Clearly communicate special instructions to packers via order management systems.
- Use visual aids or packing checklists for detailed orders.
- Implement quality control checks to verify accuracy before shipping.
Inefficient Labeling Processes
Manually labeling products or using incorrect label formats causes delays and shipping errors.
Solutions
- Automate label printing and integrate it with your system.
- Invest in automated label applicators for high-volume operations.
- Train packers on proper label placement and regularly check quality.
Poor Workflow Between Picking and Packing
Disorganized staging areas or delays in transferring items slow down the overall fulfillment process.
Solutions
- Optimize the transition of goods with designated staging areas.
- Use systems like conveyor belts or carts to streamline movement between pickers and packers.
- Develop a clear workflow to align both teams.
General Strategies for Overcoming Bottlenecks
On top of addressing specific bottlenecks, these broader strategies can significantly improve your pick-and-pack operations:
- Invest in Technology: Warehouse management systems (WMS), order management systems (OMS), and automation significantly improve efficiency.
- Standardize Processes: Clear operating procedures and consistent training reduce errors and increase efficiency.
- Train and Empower Your Team: A well-trained, well-motivated team is a critical driver of operational success.
- Measure Performance: Track key performance indicators (KPIs) such as order accuracy and pick/pack speed to
- identify issues and opportunities.
- Seek Employee Feedback: Employees often spot inefficiencies that managers might miss—they’re your best source for improvement ideas.
- Foster Continuous Improvement: Always look for ways to adapt and optimize—warehousing is no place for a “set it and forget it” mindset.
Streamline Your Fulfillment for Business Success
The pick-and-pack process is a crucial part of fulfilling customer orders efficiently. Addressing bottlenecks such as inefficient layouts, poor inventory management, and disorganized workflows can dramatically improve your warehouse’s productivity.
At APS Fulfillment, Inc., we offer full-service e-commerce fulfillment out of Miami that includes state-of-the-art warehouse management software (WMS), and we make inventory management and goods tracking easy. We’ll also support your business and automate the warehousing, prepping, shipping, picking, and packing of your orders!
Get in touch with us today to optimize your fulfillment processes and ensure every customer gets the perfect delivery—on time, every time. To book a consultation, call (954) 582-7450 or email [email protected].